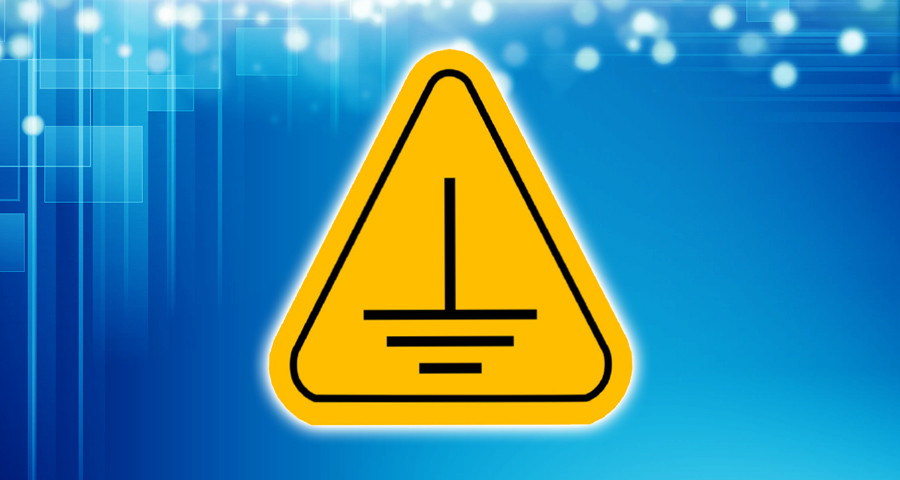
Ground is ground, right?
In truth, there is no ideal ground, all ground paths have inductance, resistance and noise. Managing the various ground paths interfacing with a high voltage power supply makes the difference between a good design and a great design.
With high voltage power supplies, ground path issues become increasingly problematic as the voltage increases. A typical high voltage power supply is programmable via a low voltage programming input, the XP EMCO CB101 model is a good example. This regulated and programmable product converts a 0 to 5 Volt programming signal into a zero to 10,000 Volt output voltage, in other words, the device has a gain of 2000 and any error appearing on the programming input will be multiplied by 2000 and show up on the high voltage output. Many high voltage systems require extreme accuracy, if the programming signal shares a ground with a power ground an error will be introduced.
Three Types of Grounds
There are typically three types of ground in a high voltage power supply system; the input power source, the low voltage control and monitoring circuits, and the high voltage return. These three grounds should have their own independent, dedicated current return paths and should be connected using a “star” grounding technique.
Input power source
The input power source will contain noise due to ripple current and will have voltage drop due to I2R losses. If a precision power supply is referenced to this “dirty” ground, error and noise will be introduced degrading system performance. The input supply and return must not share a path with the sensitive control circuits.
Output ground
The output ground can be especially problematic in high voltage systems. Stored energy (measured in Joules) equals ½ CV squared (Capacitance and Voltage) meaning that energy transferred during a high voltage discharge rises very quickly with increases in voltage. If not limited, the peak current during an arc can be destructively high.This high current surge causes voltage transients on ground paths that, if not routed properly, can destroy low voltage circuits. It is important to route the high voltage return path directly to the high voltage return on the power supply. Improper grounding techniques can result in field reliability problems due to high voltage discharges.
Poor performance and field failure
Many high voltage applications require precision and low noise. The CB101, mentioned above, features ripple and regulation of less than 0.1% at 10,000 volts. In addition to the 0 to 5 volt analog programming input, this model also features output voltage and output current read-back/monitor signals, also 0 to 5 volts. Poor grounding techniques can degrade both the ripple and regulation performance and the accuracy of the monitors. For best performance, the control circuits should not share a ground with other parts of the system. The CB101 also features a plated steel case to reduce the EMI for optimal control circuit performance. The metal case is not internally connected to the circuit, giving the designer the choice to connect it to a low noise ground via the case ground pc pin.
Managing the different ground paths around a high voltage power supply is critical to realize the full benefit of the power supply’s performance potential. Failure to properly route the high voltage return path may lead to poor performance and field failure rates far below the expected MTBF.